History
The American Precision Museum combines the atmosphere of an original 19th century factory building with a world-class collection of historic machines. The 1846 armory building, the “Shaping America” exhibition and accompanying programs explore industrial history in the context of innovation, creative problem solving, and the impact of precision manufacturing on American history and culture.
Robbins and Lawrence Armory
The American Precision Museum is located in the Robbins & Lawrence Armory, a National Historic Landmark located in Windsor, Vermont. In 1846, Samuel Robbins, Nicanor Kendall, and Richard Lawrence took the bold step of bidding on a government contract for 10,000 rifles. Having won the contract, they then constructed a four-story brick building beside Mill Brook. They brought in workers and mechanics, invented new machines, adapted old ones, and perfected techniques for producing interchangeable parts. Within a few years, they were exporting not only rifles but also their new metal cutting machines across North America, to England and around the world. The technology for making guns was quickly adapted to making consumer products as well as parts for many other machines.
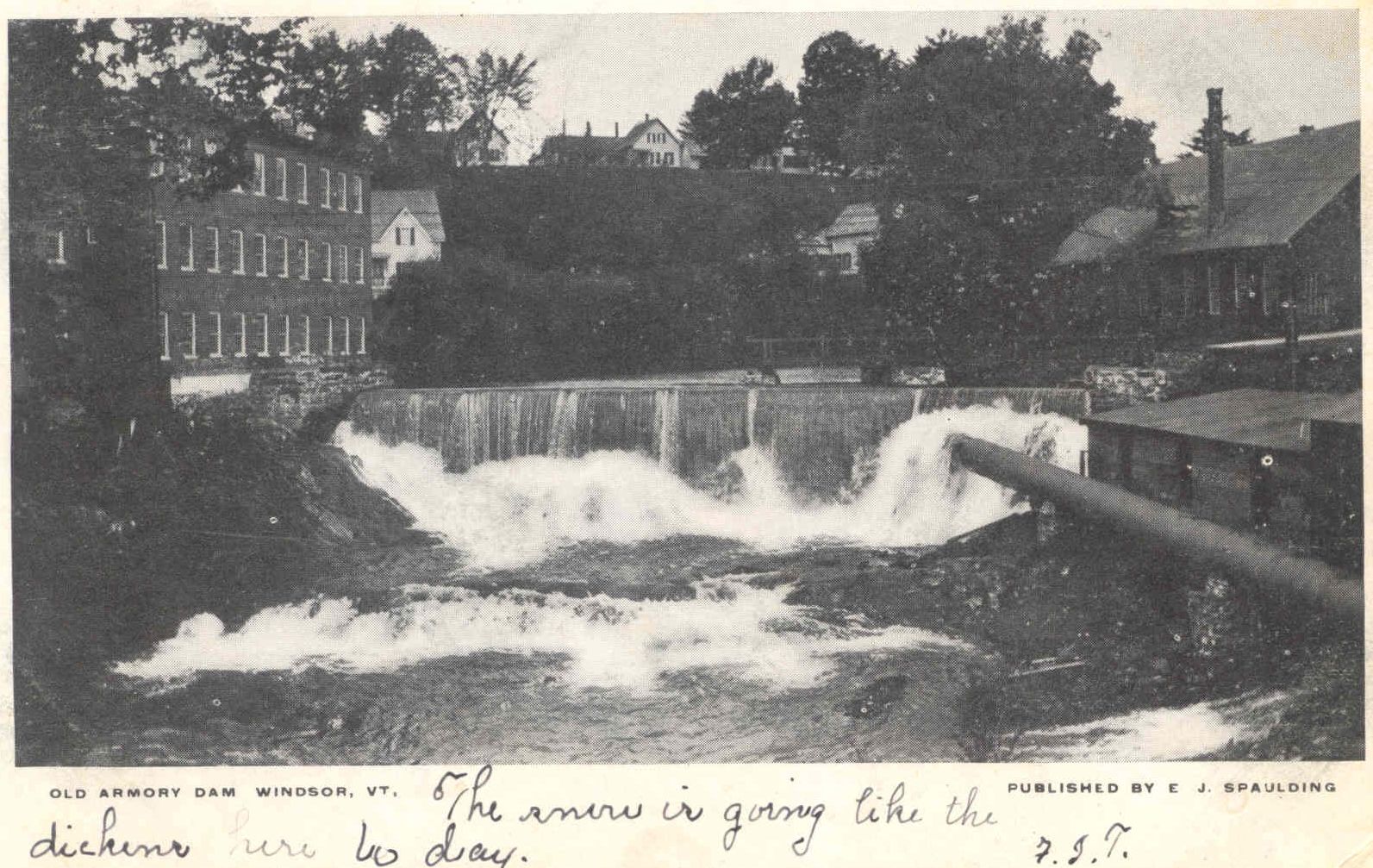
The imposing, four-story structure rises from a stone foundation adjacent to a brook that provided immediate and efficient use of waterpower. Inside, power was distributed throughout each floor with line shafting; the shafts were connected to individual machines by leather belts. Abundant windows and the building’s narrow width relative to its length (40’ x 100’), brought daylight into the interior work areas. Outside, the immediate neighborhood is still home to worker housing that was built at various times in the factory’s history. The nearby Connecticut River and the active railroad attest to the importance of transportation in the development of the site.
National Historic Landmark
The armory building is significant for its architectural integrity, which reflects the size, scale, and operation of a 19th century factory. A National Historic Landmark, in 2001 it was designated a special project of Save America’s Treasures; in 2003, APM received a Save America’s Treasures award of $200,000 for installing a new slate roof to replace the deteriorated original. The museum was designated an International Heritage Site and Collection by the American Society of Mechanical Engineers in 1987. For each of these designations, the armory was considered a site where pivotal events occurred in the history of American industry, as well as a place that lends itself to comprehensive interpretation of that history.
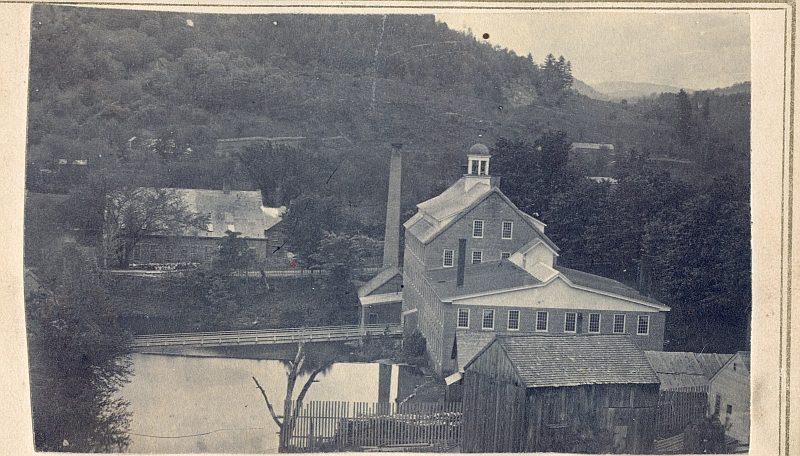
Early Manufacturing and the “American System”
The first phase of the Industrial Revolution was introduced in America during the late 18th century and was modeled on the English system of textile manufacturing. In 1846, when the Armory was built, the second phase of the Industrial Revolution—the “American System”—was about to be launched. In the remote village of Windsor, entrepreneurs and artisans had already constructed a series of dams that powered sawmills and a gristmill on the Mill Brook, 18 buildings and shops in total. In these small workshops, inventors developed designs for new products as well as making both new and old items more quickly. In Windsor and other towns up and down the Connecticut River Valley, new industries attracted more people and stimulated the creation of commercial downtowns. Mills, stores, and homes were clustered between the river and the steep hillsides.
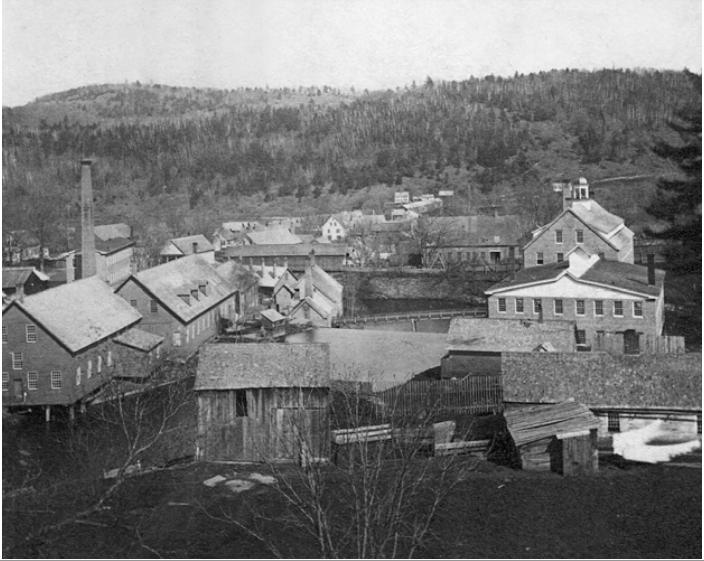
American contractors and manufacturing firms such as Robbins and Lawrence and Colt exhibited at the Crystal Palace Exhibition in 1851. (This event, officially known as the “Great Exhibition of the Works of Industry of All Nations,” was the first World’s Fair.) A few years later, the British Parliament sent a group to study the ‘American System’ of interchangeable manufacturing and to secure the machinery necessary to introduce the system at the Enfield Armory near London.
What’s the American System of Manufacturing? It depends who you ask, and Generally speaking, these elements are included:
- Division of labor: Instead of one craftsman making each part by hand, machine tools (and jigs) were used for different operations. Semi-skilled workers could then run a machine that would make the same part in the same way.
- Interchangeable Parts: “Component parts of pistols are to correspond so exactly that any limb or part of one pistol may be fitted to any other pistol of the twenty thousand,” is what a US Government Contract (the first to specify ‘Interchangeable Parts’) said to Simeon North. In order to be sure that parts are in fact interchangeable, measurement and quality assurance is required.
- Mechanization: “Machine Tools were designed specifically for each operation. Robbins & Lawrence’s contract for the Enfield machinery included universal millers, standard millers, doublemillers, screw millers, clamp millers, four-spindle drillers and machines for tapping, edging, grooving, squaring, threading, chucking, broaching, saw-slotting, screw-pointing, screw-clipping, punching, index-milling, turning and rifling,” said Edwin A Battison in his book “From Muskets to Mass Production.”
- Machines as a Resource: In his report to Parliament in 1854, a British commissioner stated that Americans use machinery whenever possible. “Wherever it can be introduced as a substitute for manual labor, it is universally and willingly resorted to.” Additionally, “the returns on [machinery investments] are calculated not merely in the narrow sense of money but in the wider sense of adding to the firm’s general resources and improving the working conditions of the staff.” (Freight Handling, 49, 50., cited in The Social Basis of the American System of Manufacturing. )
David Hounshell states in his book “From the American System to Mass Production” that the term “American System” was more often used in retrospect, looking back at the 1800s, than it was used at the time.
The Armory: 1866–1964
The building operated as a cotton mill beginning in 1866 for nearly two decades, before returning to manufacturing machine tools in 1888. Ten years later the property was sold to the Windsor Electric Light Company, before being sold to the Central Vermont Public Service Company in 1926. In 1964, CVPS proposed razing the building, prompting Smithsonian curator and Windsor resident, Ed Battison to formulate plans for the creation of a museum. Battison had a relationship with CVPS, storing various items in the building since the 1950s.
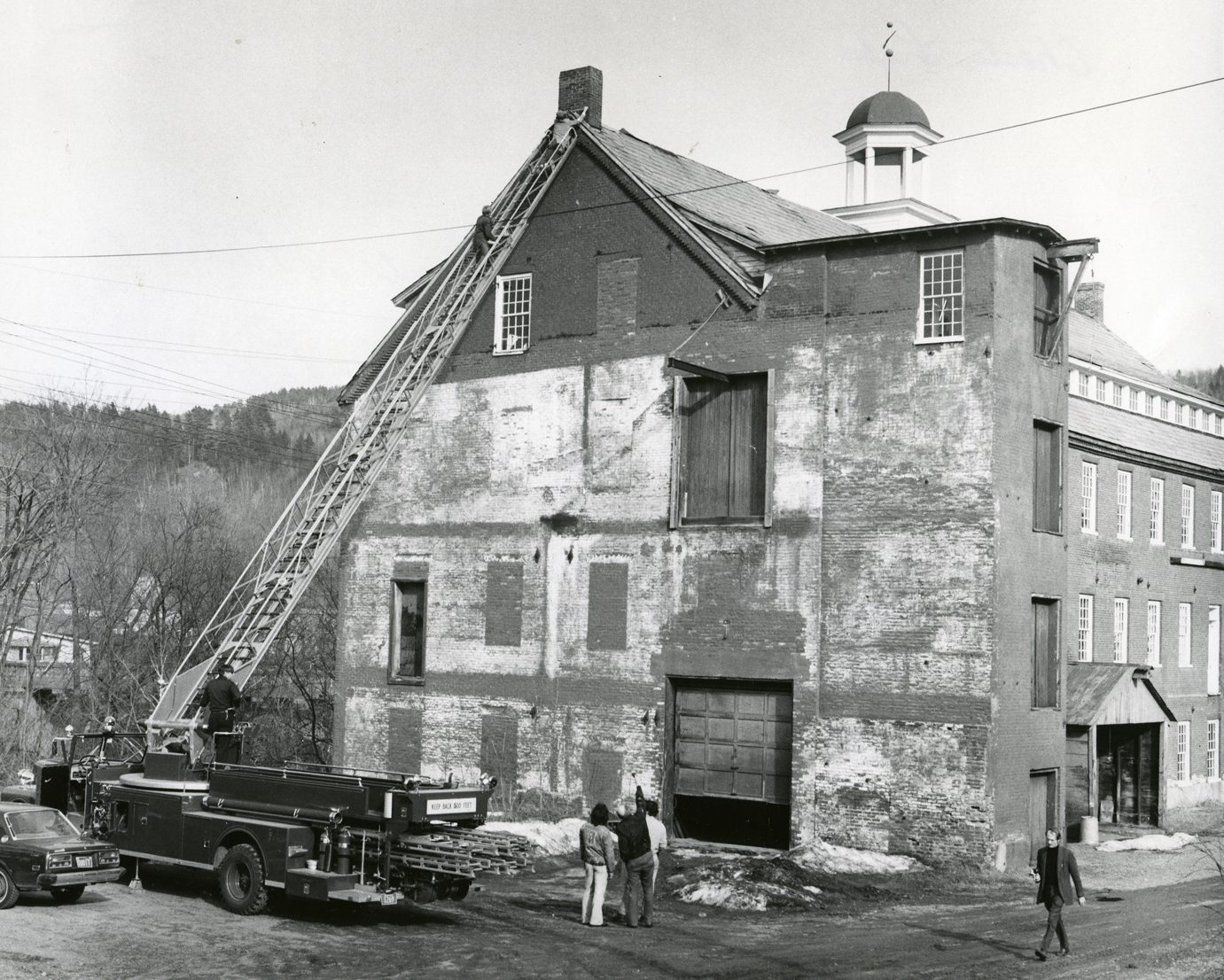
American Precision Museum Founder, Ed Battison
Windsor native Edwin A. Battison founded the American Precision Museum in 1966 and served as its director until 1991. Battison, a curator of Mechanical Engineering at the National Museum of American History at the Smithsonian Institution, secured the Robbins & Lawrence Armory to house the museum and the world-class collection of historic machine tools, related books, and archival materials he had collected during his lifetime.
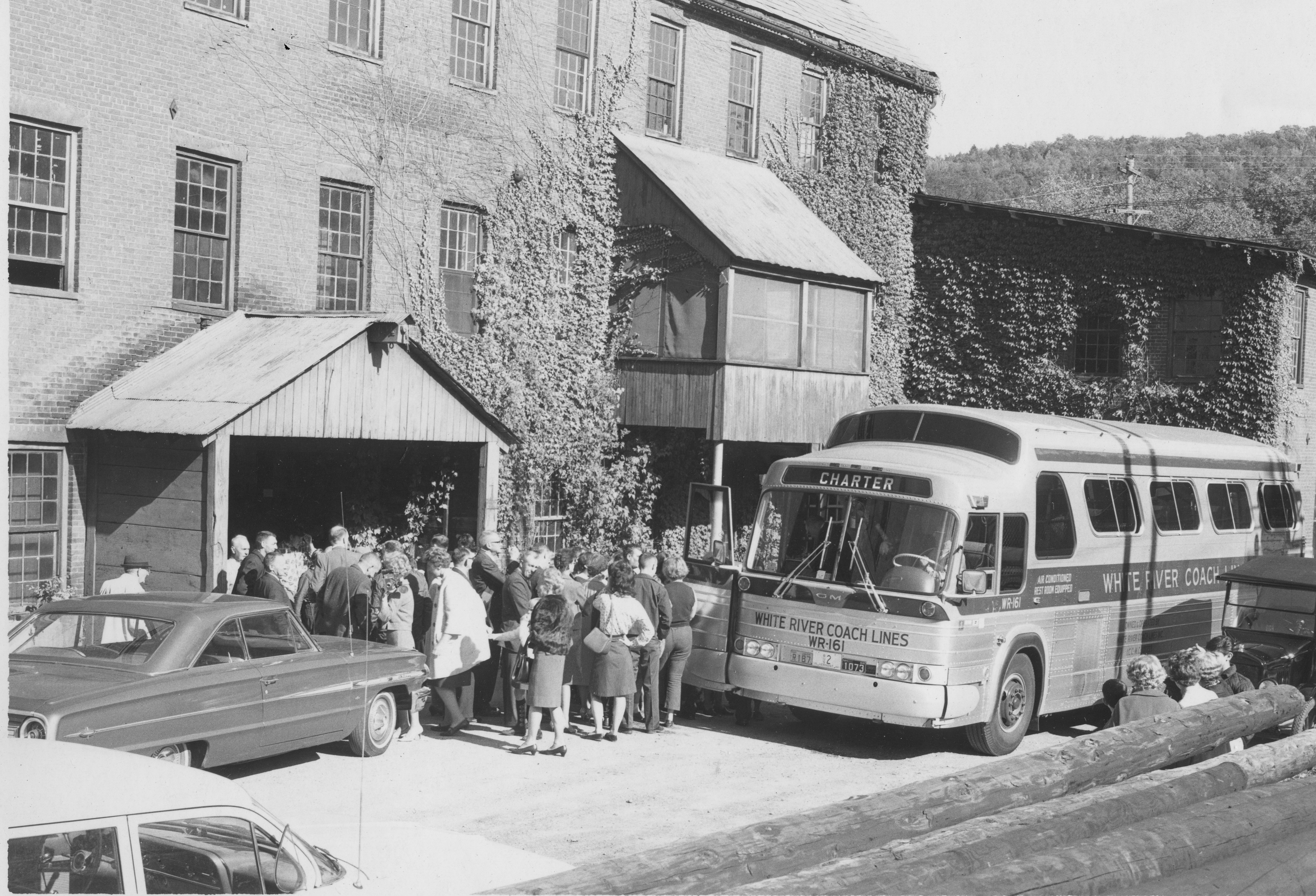
A New Era
In 1999, new leadership began professionalizing the operations, preserving the physical assets, and marketing to a wider audience. APM undertook a major restoration effort, installing a new slate roof, completing interior structural repairs, restoring two-thirds of the historic wood windows, re-wiring the building, updating security and fire detection systems, and launching a masonry restoration program.

Shaping America: Machines and Machinists at Work
This 4,000 square-foot exhibition focuses on the people whose work made great societal changes possible and the rise of the “American System” of manufacturing. “Shaping America” is the first comprehensive exhibition to examine Vermont’s industrial history in-depth and explores the broad themes of innovation and problem solving, craftsmanship, and the influence of precision manufacturing upon American history and culture. Precision manufacturing reinforced the growth of the American middle class and laid the foundation for the consumer culture that developed during the 19th and 20th centuries.
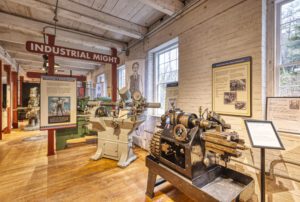
Generous support from the National Endowment for the Humanities helped make this exhibition possible.
Windsor, Vermont and Precision Manufacturing
Windsor, Vermont, the home of the American Precision Museum, played an important role in the development of precision manufacturing and the machine tool industry in America. The Robbins & Lawrence armory served as a breeding ground for innovation in the mid-19th century and as a center for excellence in the high tech industry of its day. Military leaders and industrialists traveled to Windsor to learn about the new “American System” of manufacturing, and workers from Windsor were aggressively recruited by other emerging industries. By continually increasing productivity, the machine tool industry spread the notion that material abundance was possible for a broad cross section of the American people. At its full maturity in the mid 20th century, the machine tool industry provided the backbone of American industrial strength and helped the United States develop into a world power.
Collection and Archives
The museum’s holdings include an unparalleled collection of industrial machinery spanning the first one hundred years of precision manufacturing, along with fine examples of early machined products including rifles, sewing machines, and typewriters. Photographs and archival records provide additional resources for interpreting this critical phase of the Industrial Revolution.
Mission
We engage audiences in the stories of human ingenuity through the lens of manufacturing —learning from yesterday, exploring today, and imagining tomorrow.
Vision
All will feel inspired, capable, and welcomed to participate as problem solvers and innovators to help make a positive difference in the world.
What We Value
Sense of Place
We take pride in our historic roots as a birthplace of precision manufacturing, our influence on the evolution and growth of the Nation’s manufacturing industry, and our role in industrial history.
Innovation—Past, Present & Future
We believe the future of innovation is inextricably linked to the past, including our deep, rich history and impact on the evolution of manufacturing in America and abroad. Our collections and programs highlight the work of manufacturers and the industry’s continued innovative solutions and contributions to society.
Joy of Making
We believe that everyone can engage in making and manufacturing and should have opportunities to be immersed in hands-on problem-solving and innovative thinking. The act of making and producing provides opportunities for creativity, inventiveness, skill-building, contribution, pride, and joy.
STEM + M
We create engaging and relevant STEM learning experiences in our programs, exhibition galleries, and online resources that directly connect with manufacturing technologies and careers. At APM, we add a second M, for Manufacturing, to the acronym for Science, Technology, Engineering, and Mathematics.
Interconnection
We share how manufacturing and innovation are both an influencer to and influenced by our history, culture, and economy. We take pride in using our historic collection to weave together the stories of the people involved in these innovations across time and technologies.
Inclusive and Welcoming
We strive to create experiences that are inclusive and relevant to everyone and aspire to provide an environment that is welcoming, accessible, and inspiring.
Collaboration
We find success for all through collaborations with our local, regional, and national community members and organizational partners.
Board
Board of Trustees
- Chet Birger, Tilton, NH
- Rob Caron, Wells, ME
- Christopher Gray, Springfield, VT
- Eric Hagopian, South Deerfield, MA
- Greg Jones, McLean, VA
- Greg Kaufman, Washingtonville, NY
- Richard Kline, Cincinnati, OH
- Lee Morris, Windsor, CT
- Lorraine Palmer, Punta Gorda, FL
- Larry Schwartz, Clear Spring, MD
- Don Thomas, New London, NH
Interested in becoming more involved? Give us a call at 802-674-5781!
Staff
Steve Dalessio – steve@americanprecision.org
Executive Director
Steve joined APM as the new Executive Director in September 2019. Prior to becoming the Executive Director he served as both Chair and Vice Chair of the Executive Committee. Steve has held leadership positions in medical device, aerospace, and defense manufacturing. For the past 17 years he has been General Manager and a Partner in a local precision machining company. Steve is committed to volunteerism in his local community where he serves as an elected official and on other local and regional boards. In his free time he enjoys photography, local history, and is a Maker.
Dave Eastman – deastman@americanprecision.org
Director of Development and Communications
Dave comes to the museum with ten years of fundraising experience in education, the environment, and the arts, all in the Upper Valley. Prior to that he had careers in marketing and communications, and also as an educator, primarily teaching history. His interest in the museum comes from his experience in history and education, as well as a family connection to the manufacturing world. His family owned a small machine tool company in Indiana, and his father worked in the manufacturing sector for his whole career.
Dave and his wife raised a family over the past 25 years in nearby Hartland, Vermont. He enjoys traveling with his wife and spending time fly fishing with his two grown children.
Lisa Yordy – lyordy@americanprecision.org
Visitor Services Manager
Lisa hails from Brooklyn after a stint down South and ended up in beautiful Vermont. She has a multi-versatile background in banking, marketing, real estate and innkeeping so why not a Museum? Lisa now knows what a Bridgeport is, although the learning curve was pretty steep on that one. She feels she has found her calling as the Visitor Services Manager, doing everything to keep the visitors engaged. Lisa loves to travel, running around on her Scooter and never passes up a Newfoundland Dog that she won’t kiss!
John Alexander – jalexander@americanprecision.org
Collections Technician
I’ve been in the museum business for about twenty-nine years! At the Montshire Museum, it was almost exclusively in exhibits. At American Precision Museum, it’s been a great variety of responsibilities.
Among my great joys are getting a new exhibit well-lit and moving the big machines around. Another wonderful thing has been relating with volunteers. I’ve worked with remarkable people. I’m currently working on recording descriptions and taking photos of all the items in our collections, and that’s exciting too.
Extracurricular activities? Well, I have children and grandchildren in the area. I go out to listen to jazz. Also dance to rock and roll and sometimes swing.
Molly Holleran – mholleran@americanprecision.org
Education Specialist
Ten years ago Molly worked as an intern at the museum demonstrating on the historic machines and interacting with visitors. She went on to get a degree in English and Philosophy and taught in public and private schools for a number of years before coming back to teach in Vermont at the start of the pandemic.
In an unexpected turn of events she found herself back at the museum, this time to work as an educator, bringing STEM education to local schools. She initially visited the museum with family and considered volunteering but when she realized there was a career opportunity here she knew she had to take it.
When not at the museum she enjoys sewing and pattern design, singing and playing the violin, and tinkering with mechanical watches. She also speaks a little French which comes in handy with visitors and any time she needs to order food in France.
Devon Kuhrau – dkuhrau@americanprecision.org
Development Associate
A South Carolina native and graphic designer by trade, Devon is equally new to New England and nonprofit development. She initially visited the museum as a tourist and fell in love with the building and the collection. Seven months later, in July 2022, she joined the APM team. Excited about the future of the museum, she is cultivating relationships with our donors and members and still designing graphics here and there. She also speaks German, which has come in handy with German visitors to the museum.
When she isn’t at the museum, Devon enjoys knitting, camping, and exploring Vermont and New Hampshire.
Jerry Rex
Director of Corporate Development
Jerry joined APM with over four and a half decades of experience in various roles in manufacturing. Starting as a machinist apprentice at GE he then had stints in engineering, sales and company leadership, including the last 20 years as president of various distributor organizations. Jerry served on the board of directors of AMT, culminating in his role as Chairman in 2015-16. Viewing the museum as a way to help raise awareness of the opportunities in manufacturing, Jerry joined us to work directly with industry leaders and companies who have a vested interest in inspiring the next generation of makers. He also views this as a way to give back to the industry that has blessed him and his family.
Jerry and his wife of 35 years live outside of Cincinnati, Ohio and he is an avid outdoorsman, as well as a lover of music, sports and lifelong learning.
Jobs at APM
The American Precision Museum in Windsor, Vermont, is looking for talented people to join our team.
Located in the 1846 Robbins & Lawrence Armory, a national historic landmark, innovation is at the heart of the museum. Our exhibits tell the story of innovation in manufacturing technology – past, present, and future. Interactive STEM educational programming is designed to inspire the next generation of innovators.
Please take note of how to apply & ask for more information; this may vary based on the position.
The American Precision Museum in Windsor, VT, seeks a skilled, experienced, and passionate STEM educator to lead the museum’s efforts in implementing and broadening its portfolio of programs while maintaining an active teaching role. This position will manage and supervise staff and contract educators while overseeing all program development and delivery. The Education Manager will implement new programs serving youth outside of school hours, develop and coordinate programs for adult learners and educators, and collaborate with others to create museum-wide special events and festivals. In addition, this position will be responsible for managing large educational projects, including the museum’s current STEM+M (STEM+Manufacturing) Pathways Project, and collaborating with the Director of Development and Communication on proposal development and program marketing needs.
The successful candidate filling this position will possess expertise in STEM and maker education with a passion for the mission of the American Precision Museum. They thrive in collaborative, team-oriented, mission-driven environments while bringing their creative energy to help grow an organization to best meet the needs of the communities it serves. They will appreciate the historic story told by the museum through its exhibits and collection and strive to create programs and learning experiences that connect the past with the present in meaningful and relevant ways that engage all learners. They enjoy working with audiences of different ages and backgrounds and leading open-ended learning experiences. The successful candidate will be an expert facilitator and communicator who cares deeply about creating inclusive and welcoming experiences for all.
This position is full-time, exempt, with benefits. Salary range $60,000–$70,000
Annual Reports
Community and Memberships
The museum is a member of local, regional and national organizations, including:
- American Alliance of Museums
- American Association for State & Local History
- National Association of Reciprocating Museums
- Blue Star Museums
- Distinctive Destinations of the National Trust for Historic Preservation
- Hartford Area Chamber of Commerce
- New England Museum Association
- Vermont Historical Society
- Vermont Curators’ Group
- Vermont Attractions Association
- McAuliffe-Shepard Discovery Center Partner Program
- Society for Industrial Archaeology (New England Chapters)
- Woodstock VT Chamber of Commerce
Partners
The commitment and generosity of our partners support our efforts in preserving the 1846 Robbins & Lawrence Armory, a National Historic Landmark, our extensive collection of historically-significant machine tools (largest in the nation), and our exhibits and daily programs—including the new Learning Lab and Innovation Station.
Does your support really make a difference? Yes!
Memberships and Donations contribute significantly to our annual operating revenue. With your generous support, APM will continue to expand our educational and career awareness programs.
CORPORATE PARTNERS
We are grateful for the dedicated support of our corporate supporters and industry friends, listed below, that have been instrumental in advancing APM’s mission: telling the story of the machines and the people that formed the foundation and advance the future of American manufacturing. These companies carry on the tradition of innovation and excellence developed during the mid-19th century here at the Robbins & Lawrence Armory and by our counterparts in the Precision Valley.
Ambassador Level
Leader Level
Partner Level
Patron
Advance Welding
Belt Technologies
Big Daishowa
Coastal Safety LLC
Edge Technologies
Griggs Steel
Horst Engineering
Ingersoll Machine Tools
Kansas-Oklahoma Machine Tool Inc.
Machine Tool Specialties
Pre-Tech Precision Machining
Predator Software, Inc.
Sturm, Ruger and Company, Inc.
Tri-Angle Metal Fab
EDUCATION PARTNERS
The American Precision Museum has developed strong partnerships with many institutions, organizations, and businesses that support our goal to develop new programs, engage students and families, and improve access to STEM education. We collaborate with various organizations to enhance learning opportunities for our visitors and community.
Education Partners include:
SparkShop empowers students to apply their skills to engineering challenges and see their value in STEM fields.
The curriculum contains a dynamic mix of experiments, discussions, demonstrations, and problem-solving designed for 4th-5th graders. We aim to build the initial enthusiasm
that prepares students to pursue the STEM activities later in their learning careers.
The River Valley Technical Center offers an education that prepares students to be career and college ready. Students learn technical skills in their program areas, employability skills that prepare them for the workplace, and academic skills, including math, reading, writing, science, or social studies. Employers are looking for employees who can utilize technology, solve problems, and work effectively in teams. The River Valley Technical Center affords high school students and adults the chance to learn these skills through practical, hands-on experience so they are better prepared to take advantage of further learning and career opportunities.
Homewood Science Center is a nonprofit community science center founded in 2016 to serve Chicago’s culturally and economically diverse south suburbs. Their mission is to inspire scientific wonder, learning, and pursuit. They work with educators, STEM professionals, and partner organizations to increase STEM literacy and foster diversity, equity, and inclusion in STEM, so all area students can gain the skills and confidence they need to fully enjoy and contribute to the civic and commercial vibrancy of their region.
APM in the News
Vermont Business Magazine – APM Vision Event
New England Magazine: 10 Events to Visit in Vermont this Summer
WCAX: Vermont museum looks to the past to help create jobs of the future
Valley News: Windsor museum gets funds to renovate, expand STEM programs
Eagle Times: “APM Receives $500,000 Grant”
APM Featured in Image Magazine
Image Magazine featured the American Precision Museum in the summer 2022 issue.
Thank you, Image! You can see the spread here or pick up a copy of Image locally.
Eagle Times: “Dream Big about Their Future”
“WINDSOR, Vt. — Rosie’s Girls Invent, a STEM forward camp for young girls and gender expansive youth alike, has come to Windsor, Vermont. The camp will be held on site at the American Precision Museum once a week until August 23rd and aims to teach young people skills in STEM fields, engineering, and also socio-emotional skills to help propel them to success.”
Mastercam Announces Exhibit Partnership with Haas and the American Precision Museum
September 22, 2020 (Tolland, Conn.) – CNC Software, Inc., developers of Mastercam, the world’s leading CAD/CAM software, has announced a new partnership with the American Precision Museum (APM) and Haas Automation. APM combines the atmosphere of an original 19th century water-powered manufacturing facility with a world-class collection of historic machines. It explores industrial history in the context of innovation, creative problem solving, and the impact of precision manufacturing on American history and culture.
The APM factory was first powered by a great water wheel, located in the basement, which drove a drum that carried belts up through the ceiling to the overhead line shafts on the factory floor. Those shafts turned smaller belts that powered the machines. APM is partnering with Mastercam to recreate a waterwheel to have on display in the museum demonstrating how running water was turned into power to drive the building.

The Applications Engineers at CNC Software, Inc. designed a functional scaled-down version of the original waterwheel found at APM. To keep it as realistic as possible, the model design was inspired by a 2009 study of the original factory and wheel. The assembly was designed in Mastercam for SOLIDWORKS® and programmed and machined using Mastercam. Most of the assembly is made from ¾” prefinished plywood and was machined down on a 3-axis router. The mechanical components are aluminum and steel and machined on a Haas VF2 CNC, taking waterwheel power into the 21st century.The scaled-down version has a working drive gear assembly, and for display purposes is not powered by water but instead uses a small pellet stove gear motor.
“CNC Software is proud to partner with the American Precision Museum. APM is helping to tell the story of how mass production changed the world and shaped America,” says Meghan West, CEO of CNC Software. “APM is looking to recreate a waterwheel, and we are honored to help reproduce it with Mastercam. Exhibits like this are intended to spark imaginations and inspire younger generations to get involved with manufacturing. We are 100% behind that.”
Toni Neary, Director of Education for the Morris Group – Haas Division, “We are so thrilled that HFO Trident, Haas, Mastercam, and the American Precision Museum have found this way to partner and build such a dynamic project. Our organizations are committed to growth through education, sparking awareness of careers in manufacturing, and good old American ingenuity. This waterwheel is the culmination of those passions. The team at Mastercam has worked to create a fun and exciting way to discuss the history of the museum and integrated modern manufacturing technologies to replicate parts of our history. We so appreciate the time and craftsmanship in making this vision a reality.”
Steve Dalessio, Executive Director of APM, further states, “Using advanced manufacturing methods to recreate an 1846 device is a great way for us to demonstrate how manufacturing continues to evolve. We’re so grateful to Mastercam for creating this model for us, because our education program will be able to use the exhibit to link science, history, and manufacturing.” The new display will be unveiled for Manufacturing Day 2020.
For more information on Mastercam, please visit www.mastercam.com.
For more information on Haas Automation, please visit https://www.hfotrident.com/about/.
For Museum Day, Windsor’s American Precision Museum Opens Up About Manufacturing
American Precision Museum Appoints Steve Dalessio as New Executive Director
Windsor, VT, September 12, 2019. . . The American Precision Museum’s Board of Trustees is pleased to announce the appointment of Steve Dalessio as its new Executive Director. He succeeds Ann Lawless, who retired in 2018 after serving as director for 15 years. Dalessio will implement the museum’s mission and goals in innovative and creative ways, overseeing the daily operations, budget, and fundraising, in addition to refining the museum’s long-range strategy and interpretative plan.