Pop-Up Exhibits
We have a rotating selection of exhibits in the museum lobby. We call these our pop-up exhibits.
Past Exhibits:
The Art of Anna Held Audette
Mechanical Marvels
Irish Inventors
Do you have something you want to donate?
For all inquiries about donating to the museum’s collection, email Steve Dalessio at steve@americanprecision.org or John Alexander at jalexander@americanprecision.org
Digital Exhibit: Visitor Orientation Film
“Igniting Innovation: The Manufacturing Revolution in Precision Valley,” is the name of the visitor orientation film by Edge Factor . The story of Precision Valley is so captivating that the film is an official selection of the Raw Science Film Festival, and Best Documentary at the Ozark Mountain Webfest!
The Science and Technology of Measurement
Our new display demonstrates what it takes to have precision.
Featuring tools that measure speed, power, time, distance, hardness, and weight, the exhibit features Edison’s Gage Blocks, a ballistic chronograph, and more.
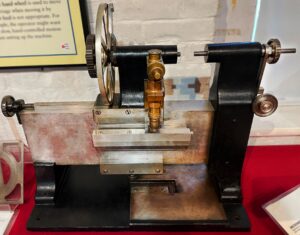
Shaping America
Our signature exhibit, Shaping America, explores how the machinists and tool builders of this region’s “Precision Valley” played an important role in determining the course of American history. The exhibit examines how advancements in machining drove industrialization, changed the face of war, and allowed for the development of our modern consumer culture.
The exhibit begins in the 1840s, right here in Windsor, Vermont, where the American System of Manufacturing was born. Combining the extensive use of interchangeable parts with mechanization of production, made this new system of manufacturing set the standard for making more products faster while using fewer resources. Discover many of the earliest machines—and the people behind them—that helped change the way the world manufactures and the way we live.
Further along in the exhibit, investigate how advances in arms and ammunition manufacturing, developed at the 1846 Robbins and Lawrence Armory, helped determine the outcome of the Civil War.
Still recovering from a divisive Civil War, the exhibit explores an era of rapid industrial innovation. Machines once devoted to creating the tools of war were repurposed for consumer goods. Machine tools and the products they created, evolved and advanced, developing into the backbone of American industry. Automobiles, planes, and countless other mechanical marvels become accessible and affordable to a broad range of consumers.
At the heart of the exhibition space, the Innovation Station brings the history of manufacturing to life. From machines over 100-years-old to state-of-the-art automated machine tools, visitors may explore the recent history of manufacturing and its rapid development. The Innovation Station offers the rare opportunity to watch these impressive machines in action and learn about the skills and training required to create, run, and maintain them. The Innovation Station celebrates advancements in machining and aims to inspire the next generation of innovators in manufacturing.
Collections Connection
Welcome to the American Precision Museum’s Collections Online!
Explore a selection from our archives, including photographs, artifacts and more.